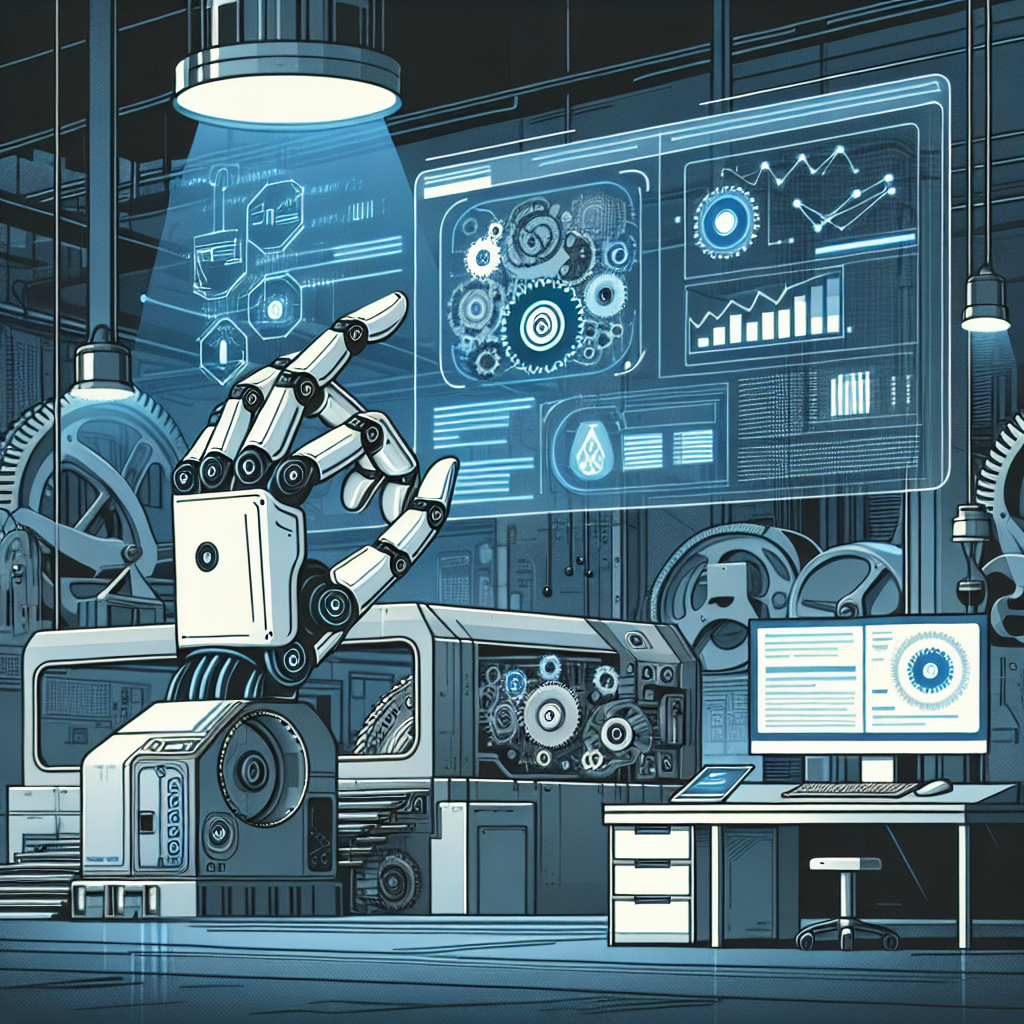
Introduction
In the industrial world, maintaining equipment efficiency and reliability is crucial. Traditionally, maintenance strategies have been either reactive or preventive. Reactive maintenance deals with equipment failures as they occur, while preventive maintenance follows scheduled checks and part replacements. However, these approaches come with drawbacks such as unexpected downtime and unnecessary maintenance. Enter the era of Artificial Intelligence (AI), which is dramatically transforming predictive maintenance for industrial equipment.
What is Predictive Maintenance?
Predictive maintenance employs advanced data analytics to predict equipment failures before they occur. By analyzing various machine parameters such as vibration, temperature, and acoustic emissions, predictive maintenance can forecast potential breakdowns. This approach ensures maintenance occurs only when necessary, significantly reducing downtime and operational costs.
The Role of AI in Predictive Maintenance
AI technologies like machine learning, deep learning, and neural networks are at the core of enhancing predictive maintenance. Here are key ways AI is revolutionizing this field:
1. Data Collection and Analysis
AI systems can collect vast amounts of data from diverse sources, such as sensors, historical records, and even weather conditions. Machine learning algorithms then analyze this data in real-time to identify patterns and anomalies that could indicate impending equipment failures.
2. Early Fault Detection
AI-driven predictive maintenance allows for early fault detection by recognizing subtle signs of wear and tear. These signs might be undetectable through human inspection but can be identified through complex data analysis algorithms.
3. Real-time Monitoring
AI technologies enable continuous, real-time monitoring of industrial equipment. This ensures that any deviation from the norm is swiftly addressed, allowing for immediate corrective measures, which is crucial for avoiding costly downtimes.
4. Optimized Maintenance Scheduling
AI systems can recommend the optimal times for maintenance based on real-time equipment condition monitoring and predictive analytics. This ensures that maintenance activities are carried out only when needed, maximizing equipment life and performance.
Benefits of AI-Enhanced Predictive Maintenance
Implementing AI in predictive maintenance offers several significant benefits:
- Reduced Downtime: By predicting equipment failures before they occur, AI helps in minimizing unplanned downtimes, which can be highly disruptive and costly.
- Cost Savings: Reducing unnecessary maintenance and extending equipment life can result in substantial cost savings over time.
- Increased Efficiency: AI-driven predictive maintenance ensures that equipment operates at peak efficiency by addressing issues before they escalate.
- Enhanced Safety: Early detection of faults can prevent accidents and ensure a safer working environment for employees.
Challenges and Future Prospects
Despite the clear advantages, AI-driven predictive maintenance faces some challenges. These include the high initial cost of implementation, the need for significant data storage and processing capabilities, and the necessity of skilled personnel to manage and interpret complex AI systems.
Nevertheless, the future prospects of AI in predictive maintenance are promising. Advances in AI technologies, greater availability of big data, and the continuous improvement of IoT devices will further enhance the accuracy and reliability of predictive maintenance systems.
Conclusion
AI is undeniably playing a pivotal role in revolutionizing predictive maintenance for industrial equipment. By leveraging the power of machine learning and real-time data analysis, businesses can enjoy reduced downtimes, cost savings, and improved operational efficiency. As technology continues to evolve, the integration of AI in predictive maintenance will become even more sophisticated, paving the way for a future where industrial equipment operates with unprecedented reliability and efficiency.